فرآیند تولید فولاد از سنگآهن تا محصول نهایی
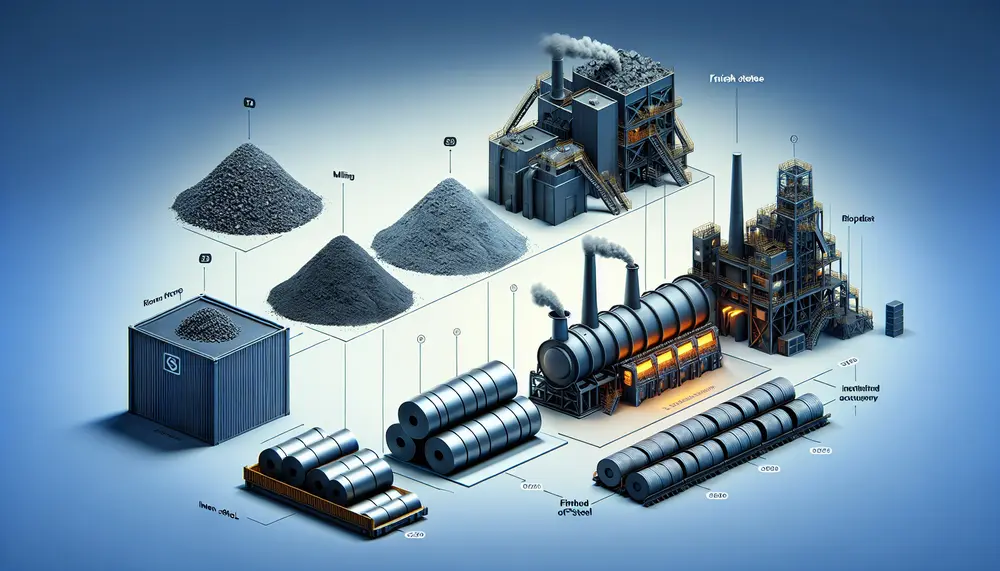
فرآیند تولید فولاد: از سنگآهن تا محصول نهایی
مقدمه:
فولاد، یکی از پرکاربردترین مواد در جهان، نقش حیاتی در صنایع مختلف مانند ساختوساز، خودروسازی، تجهیزات سنگین و بسیاری از زمینههای دیگر ایفا میکند. فرآیند تولید فولاد، سفری پیچیده و دقیق است که از استخراج سنگآهن آغاز میشود و به تولید محصولات فولادی نهایی ختم میشود. در این مقاله، بهطور جامع با مراحل مختلف تولید فولاد آشنا خواهید شد.
۱. استخراج سنگآهن
سنگآهن ماده اولیهای است که برای تولید فولاد استفاده میشود. این ماده از معادن روباز یا زیرزمینی استخراج میشود. سنگآهن بهصورت طبیعی حاوی ناخالصیهایی مانند سیلیس، فسفر، گوگرد و مواد دیگر است که در مراحل بعدی حذف میشوند. معادن مهم سنگآهن در کشورهایی مانند استرالیا، برزیل، چین و هند قرار دارند.
مراحل استخراج:
- حفاری و انفجار: سنگآهن از معادن روباز با استفاده از مواد منفجره استخراج میشود.
- حملونقل: مواد استخراجشده با کامیونها یا نوارهای نقاله به واحدهای فرآوری منتقل میشوند.
- خردایش اولیه: در این مرحله، سنگآهن به قطعات کوچکتر خرد میشود.
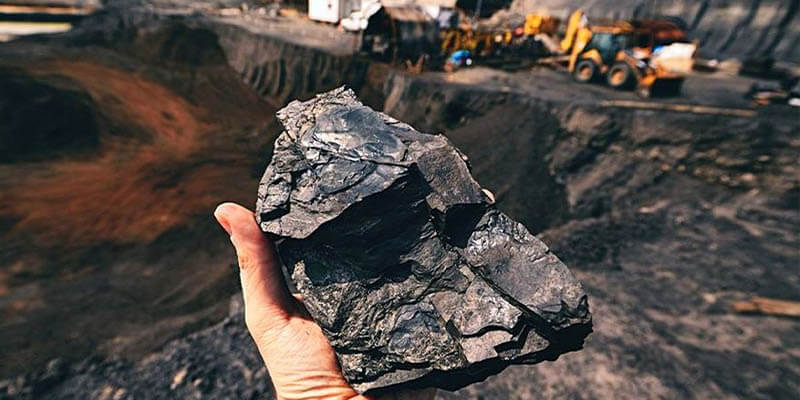
۲. فرآوری سنگآهن
سنگآهن استخراجشده باید فرآوری شود تا ناخالصیها حذف شوند و عیار آن افزایش یابد. این فرآیند شامل چند مرحله است:
- خردایش و آسیاب: سنگآهن به ذرات ریزتری تبدیل میشود تا برای جداسازی آماده شود.
- غنیسازی: در این مرحله، با استفاده از روشهایی مانند جداسازی مغناطیسی، مواد مفید از مواد بیارزش جدا میشوند.
- تولید کنسانتره: محصول نهایی این مرحله، کنسانتره سنگآهن با عیار بالا است که آماده ورود به مراحل بعدی است.
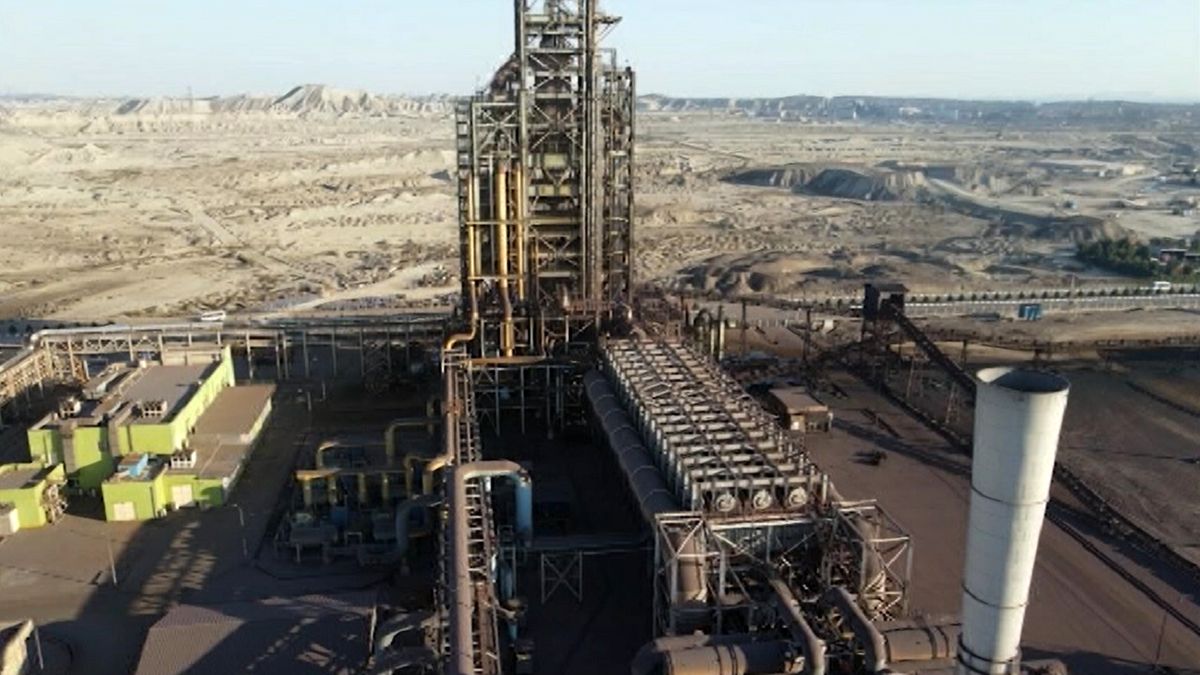
۳. تولید آهن خام (Pig Iron)
کنسانتره سنگآهن در کوره بلند (Blast Furnace) ذوب میشود تا به آهن خام تبدیل شود. مواد اولیه مورد استفاده در این مرحله شامل:
- سنگآهن یا کنسانتره
- کک متالورژیکی: برای تأمین انرژی و احیای شیمیایی.
- سنگ آهک: برای حذف ناخالصیها.
مراحل تولید:
- ورود مواد اولیه به کوره: مواد از بالای کوره وارد شده و با هوای گرم در تماس قرار میگیرند.
- احیا و ذوب: سنگآهن به آهن مذاب و سرباره (ضایعات غیر فلزی) تبدیل میشود.
- تخلیه آهن خام: آهن مذاب از پایین کوره خارج میشود و به فرآیند فولادسازی منتقل میگردد.
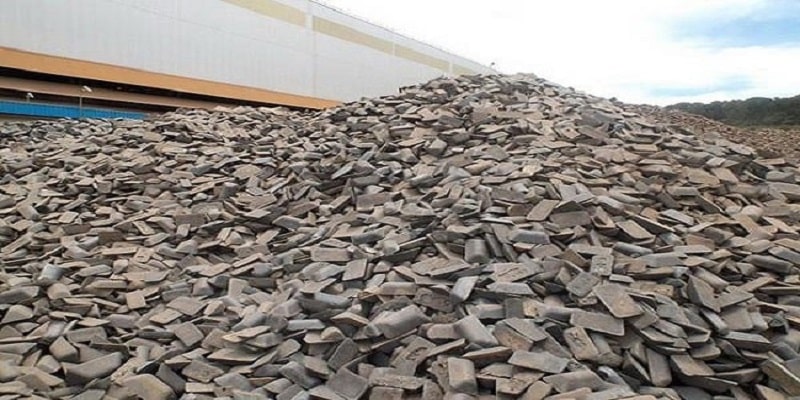
۴. فرآیند فولادسازی
در این مرحله، آهن خام به فولاد تبدیل میشود. دو روش اصلی برای فولادسازی وجود دارد:
الف) کوره قوس الکتریکی (EAF):
این روش برای ذوب قراضه فولادی و تولید فولاد نو مورد استفاده قرار میگیرد.
- مزیت: مناسب برای بازیافت و تولید فولاد با انرژی کمتر.
ب) کوره بلند (BOF):
در این روش، آهن خام مذاب با افزودن اکسیژن خالص به فولاد تبدیل میشود.
- مزیت: تولید فولاد با کیفیت بالا و در مقیاس بزرگ.
افزودن آلیاژها:
در این مرحله، عناصر آلیاژی مانند کروم، نیکل، وانادیم و مولیبدن به فولاد اضافه میشوند تا خواص مکانیکی و شیمیایی خاصی به آن بدهند.
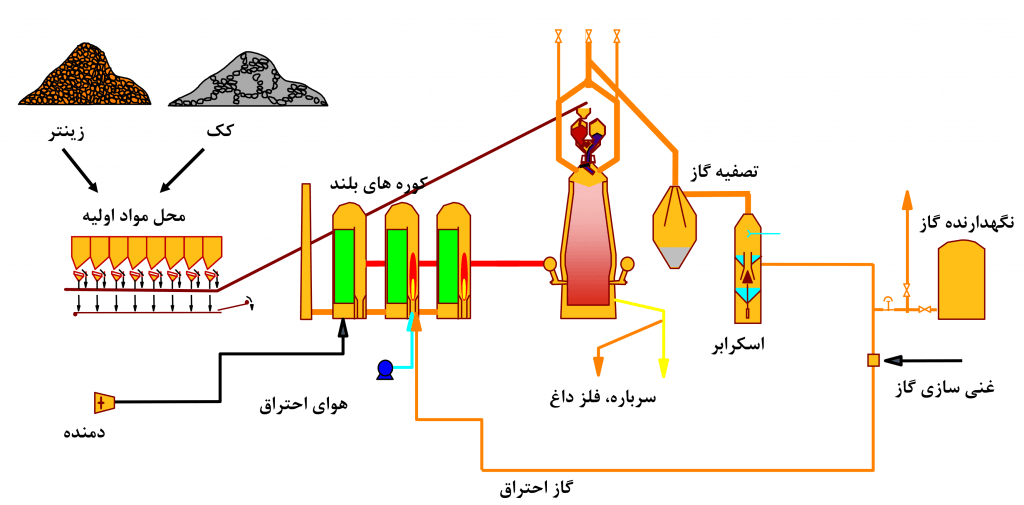
۵. شکلدهی و تولید محصول نهایی (جزئیات فرآیند نورد)
پس از تولید فولاد مذاب و تبدیل آن به شکل اولیه (شمش، بیلت یا اسلب)، فرآیند نورد آغاز میشود. نورد یکی از اصلیترین مراحل شکلدهی فولاد است که طی آن فولاد در حالت گرم یا سرد تحت فشار قرار گرفته و به اشکال و ابعاد مختلف تبدیل میشود. این فرآیند نقش کلیدی در تولید محصولات نهایی با کیفیت بالا و کاربردهای گسترده دارد.
۱. نورد گرم (Hot Rolling)
نورد گرم اولین مرحله شکلدهی فولاد است که در دمای بالا، معمولاً بالاتر از ۱۲۰۰ درجه سانتیگراد (دمای تبلور مجدد فولاد)، انجام میشود. این دما باعث میشود فولاد نرمتر شده و شکلدهی آن آسانتر شود.
مراحل نورد گرم:
- گرم کردن ماده اولیه:
- شمش یا بیلت فولادی در کورههای حرارتی با دمای بسیار بالا گرم میشود تا به دمای پلاستیسیته برسد.
- نورد اولیه:
- فولاد گرمشده از میان غلتکهای سنگین عبور داده میشود تا ضخامت آن کاهش یابد و طول آن افزایش پیدا کند.
- نورد میانی:
- در این مرحله، محصول به شکل اولیه موردنظر (مانند ورق، میلگرد، یا تیرآهن) نزدیکتر میشود.
- نورد نهایی:
- در این مرحله، ابعاد و سطح محصول نهایی به دقت تنظیم میشود.
محصولات نورد گرم:
- ورقهای فولادی ضخیم
- تیرآهن و پروفیلها
- میلگرد و لولههای فولادی
مزایای نورد گرم:
- شکلدهی آسانتر به دلیل دمای بالا
- تولید محصولات با استحکام بالا و مقاومت مناسب
- امکان تولید در مقیاس بالا
معایب نورد گرم:
- سطح زبرتر و کمدقتتر به دلیل اکسیداسیون سطحی
- نیاز به پرداخت بیشتر برای رسیدن به سطح صافتر
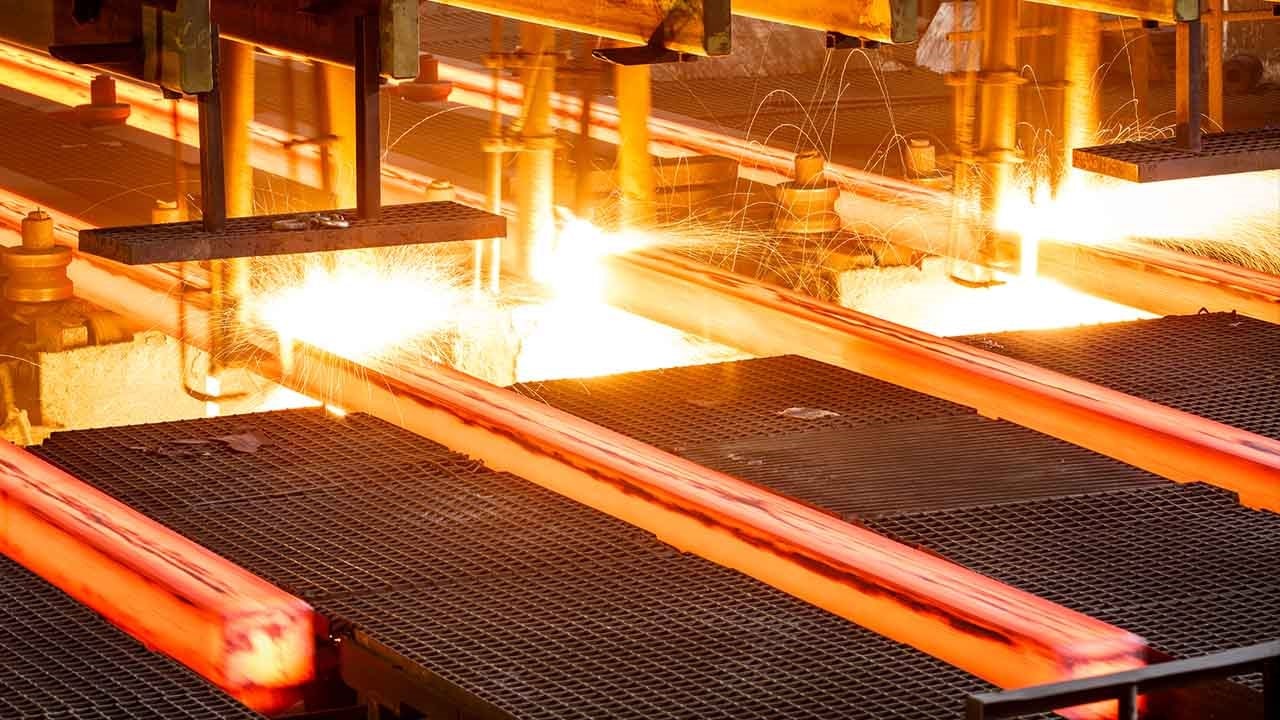
۲. نورد سرد (Cold Rolling)
نورد سرد معمولاً پس از نورد گرم انجام میشود و در دمای اتاق یا کمی بالاتر انجام میگیرد. این فرآیند برای تولید محصولات با دقت بالا و سطح صافتر استفاده میشود. نورد سرد عمدتاً بر روی ورقهای نازک و مقاطع سبک انجام میشود.
مراحل نورد سرد:
- آمادهسازی:
- محصول نورد گرم (معمولاً ورق یا کویل) ابتدا به دقت تمیز میشود تا اکسیدها و زنگزدگیها حذف شوند.
- نورد سرد:
- ورق یا ماده اولیه از میان غلتکهای بسیار دقیق عبور داده میشود تا به ضخامت و ابعاد دلخواه برسد.
- عملیات تکمیلی:
- برای بهبود خواص مکانیکی و ظاهری، عملیات حرارتی یا آنیلینگ انجام میشود.
محصولات نورد سرد:
- ورقهای نازک فولادی با سطح بسیار صاف
- لولههای فولادی دقیق
- مقاطع خاص برای صنایع خودروسازی و لوازم خانگی
مزایای نورد سرد:
- دقت بالا در ابعاد و ضخامت
- سطح صاف و صیقلی که نیازی به پرداخت اضافی ندارد
- خواص مکانیکی بهبودیافته، مانند استحکام کششی و سختی
معایب نورد سرد:
- محدودیت در ضخامت مواد قابل پردازش
- هزینه بالاتر به دلیل نیاز به تجهیزات پیشرفتهتر
۳. عملیات حرارتی پس از نورد
پس از فرآیند نورد (بهویژه در نورد سرد)، برای بهبود خواص مکانیکی، محصول تحت عملیات حرارتی قرار میگیرد. این عملیات شامل بازپخت (Annealing) و تنشزدایی است که باعث افزایش انعطافپذیری و کاهش تنشهای داخلی محصول میشود.
۴. نورد ویژه (Special Rolling)
در برخی کاربردهای خاص، فولاد باید تحت فرآیندهای نورد تخصصی قرار گیرد. برای مثال:
- نورد مقاطع پیچیده: برای تولید ریلهای راهآهن، مقاطع خاص ساختمانی و تجهیزات سنگین.
- نورد حلقهای (Ring Rolling): برای تولید حلقههای فولادی در صنایع هوافضا و خودروسازی.
- نورد فویل: برای تولید ورقهای بسیار نازک فولادی.
تفاوتهای نورد گرم و سرد
ویژگی | نورد گرم | نورد سرد |
---|---|---|
دما | بالاتر از دمای تبلور مجدد | نزدیک به دمای اتاق |
دقت ابعادی | متوسط | بسیار بالا |
کیفیت سطح | زبر و خشن | صاف و صیقلی |
هزینه | کمتر | بیشتر |
محصولات اصلی | تیرآهن، میلگرد، ورق ضخیم | ورق نازک، لوله دقیق |
۶. کنترل کیفیت و بستهبندی
در انتهای فرآیند، محصولات تولیدشده از نظر کیفیت، ابعاد، ترکیب شیمیایی و سایر ویژگیها بررسی میشوند. سپس محصولات نهایی بستهبندی و آماده حمل به مشتریان میشوند.
جمعبندی:
فرآیند تولید فولاد یکی از پیچیدهترین و درعینحال ضروریترین فرآیندهای صنعتی است که مستقیماً بر کیفیت و کارایی محصولات نهایی تأثیر میگذارد. از استخراج سنگآهن تا تولید محصول نهایی، هر مرحله نیازمند دقت بالا، فناوری پیشرفته و مدیریت حرفهای است. این فرآیند، فولاد را به مادهای تبدیل میکند که اساس توسعه صنعتی و زندگی مدرن است.
(0) کامنت
نظر خود را با ما به اشتراک بگذارید
ایمیل و شماره شما برای جواب دادن تیم ماست و به نمایش گذاشته نمیشود